It stands to reason that remanufacturing a product – rather than manufacturing a new one from scratch – saves energy. Right?
Wrong, at least according to a new study from researchers at MIT, recently published in Environmental Science & Technology [PDF].
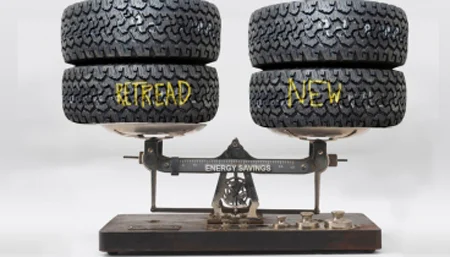
The research team, led by Professor of Mechanical Engineering Timothy Gutowski, conducted 25 case studies on products in eight categories.
They found there are indeed cases where remanufacturing saved energy, but just as many cases where remanufacturing actually cost more energy than it saved. And for the majority of the products, the savings were negligible or the energy balance was too close to call.
These results rock the boat of conventional wisdom on the subject because they account for each product’s life cycle analysis – i.e., the the total energy used by the product over its lifetime – rather than just the energy used during the manufacturing process itself.
In nearly all the cases studied, it costs less money and less energy to remanufacture a product from the recycled part of an old one than to start from scratch.
But many of these remanufactured products turn out to be less energy efficient than their newer counterparts, so the extra energy used over the product’s lifetime cancels out the energy saved during the manufacturing process.
A familiar example is retread tires. It’s true, they take less energy to manufacture than their new counterparts, but their rolling resistance might turn out to be just a bit higher, which would mean their energy advantage is eaten up by the extra gas used while driving on them.