Dwellings fashioned out of used intermodal shipping containers continue to spread into new places. Their spread is slowed by the resistance of many US cities to altering their building codes.
A three-story home made of five stacked containers, said to be the first in New York City, finally won approval for occupancy this February.
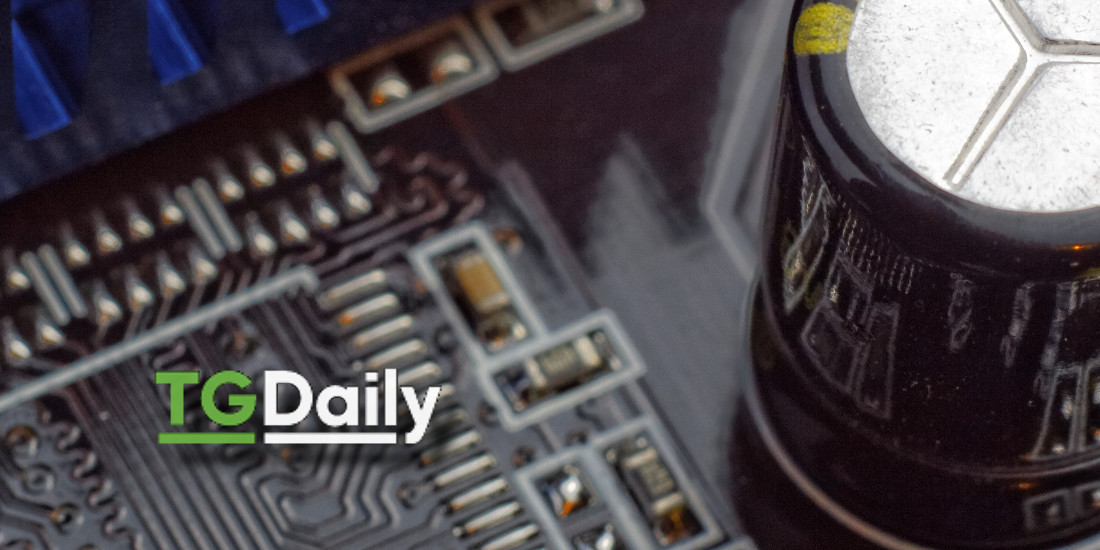
A home built from five shipping containers in Williamsburg, New York City. Via Ben Fractenberg, DNAinfo.
It was built by an architecture professor and her contractor husband after their initial plans to build on the 20-by-40 foot site began to look too expensive. A tiny conventional structure was coming in at almost $500,000; the shipping container home cost only $300,000 to build, they say, plus another $100,000 for costs incurred by having to wait and struggle for the approval from the Department of Buildings. It looks charming inside.
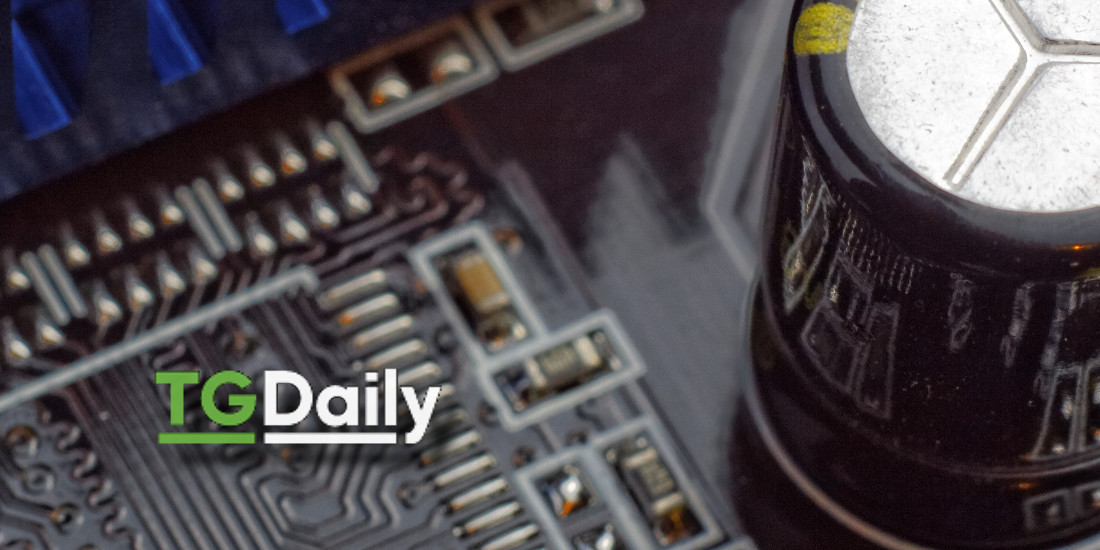
Mixed-use retail/residential proposal for St. Louis. Via Anthony Duncan Architect.
Out in the heartlands, a proposed mixed-use building in a desultorily recovering neighborhood of St. Louis is also described as a first of its kind for that city. In the rendering, you can see how 3-plus-3 larger containers are stacked atop four somewhat smaller ones, projecting out in front so as to shelter a small entry plaza. The plan is for retail on the ground floor, residence(s) on the top floor, and either offices or more space for the retail tenant in the middle.
Turning containers into buildings is ballyhooed as green architecture. To be honest, I’m going to have to see some hardcore life cycle analysis before I go along with it. Sure, they’re upcycled, but it takes a lot more than that to make sustainable architecture. Maybe this is what we get for decades of passing off recycling as the very essence of environmentalism.
The New York City cargo house is said to be insulated by its paint. Man, that’s thin insulation! Something high-tech called Super Therm. It’s hard for me to see how you can save money building a properly insulated house for New York’s climate by starting out with your main structural element being highly conductive of heat and designed with absolutely no consideration of how it works together with insulation materials. Containers are more plausibly green in a climate like the Bay Area that doesn’t need much heating or cooling.
The cargotecture trend likely wouldn’t be happening without the huge surplus of containers in North America resulting from our trade imbalance with Asia. Not only do we import more than we export, but a lot of our imports are small manufactured goods, whereas our top exports are either bulk cargo (like wheat) or cargo too bulky to fit in containers (like jetliners and Caterpillars). Surprisingly, container buildings have alsoturned up in China. Go figure.
Anyway, there’s no question that containers are overabundant and artificially cheap in North America. Still I wonder if it wouldn’t be “greener” to melt them down for wind turbines and high-tension towers—or for construction studs if steel is such a great framing material.
Containers are inherently stackable. That’s especially appealing to people who want their structure to go up quickly. Modular prefab construction also goes up quickly, and high-end prefab has obvious aesthetic advantages over containers. However, modular prefab has trouble, so far, with getting to the point where it’s cheaper than comparable stick-built construction. Maybe one bright side of the cargotecture trend is if it throws down a gauntlet to the prefab industry: just try and match our costs, while beating us on aesthetics and operational energy demand.