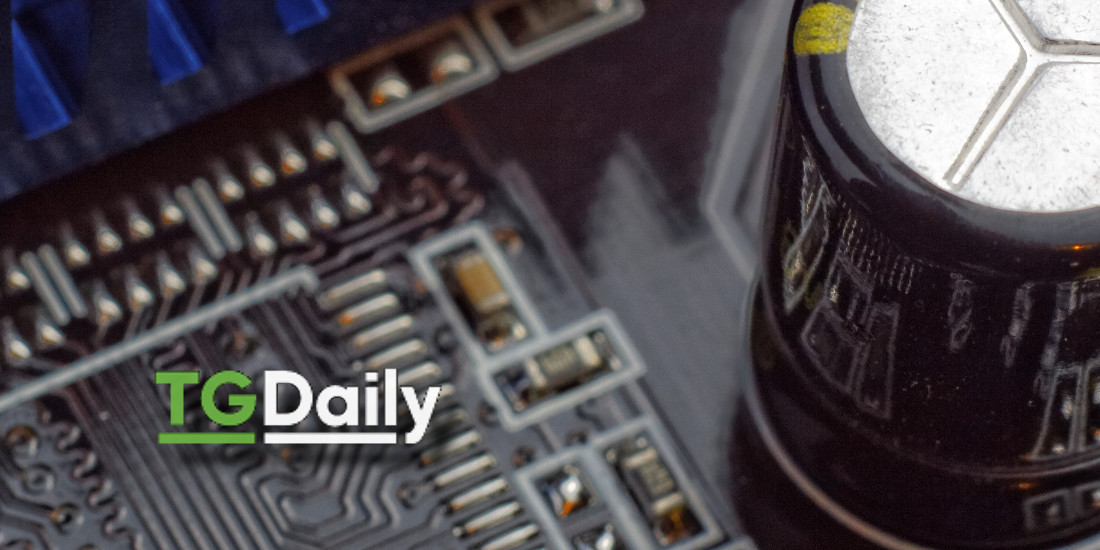
An innovative pioneer of connected medical devices, Withings offers an ideal case study of how integrating additive manufacturing into the development process can result in a healthy business Since 2009 Withings has been manufacturing a range of life-style friendly health devices, each wirelessly connected through smart phones and computers to create a well-being eco-system comprising more than 100 partner apps and services. Its most recent product, the Smart Body Analyzer integrates a new air quality sensor that checks the indoor air quality through metrics such as temperature and Co². The tracking app builds a Co²-level graph and makes users aware when important thresholds are reached. The company has integrated 3D printing as a strategy early on in its rapid prototyping process, saving money, energy and eliminating risk. “In the development process, there are always phases during which we use 3D printing. It’s really helpful to have physical pieces in your own hands in order to make the right choices. “It’s also a way for us to add the sense of touch to the visual perception. Designers often create a design just as we describe it to them, but after seeing it for real, we notice that we need to change something. In the long run, 3D printing processes have a profound impact on the quality of our products.”