You may have heard some shouts and rumors about this new technology called 3D printing.
You may even have seen some fascinating objects that have been created using this tech (such as, say, this funky little wearable planter). But unless you’ve been following the progress of this breakthrough design and fabrication process closely in recent years, you may not yet have grasped the sheer scope of its significance and potential.
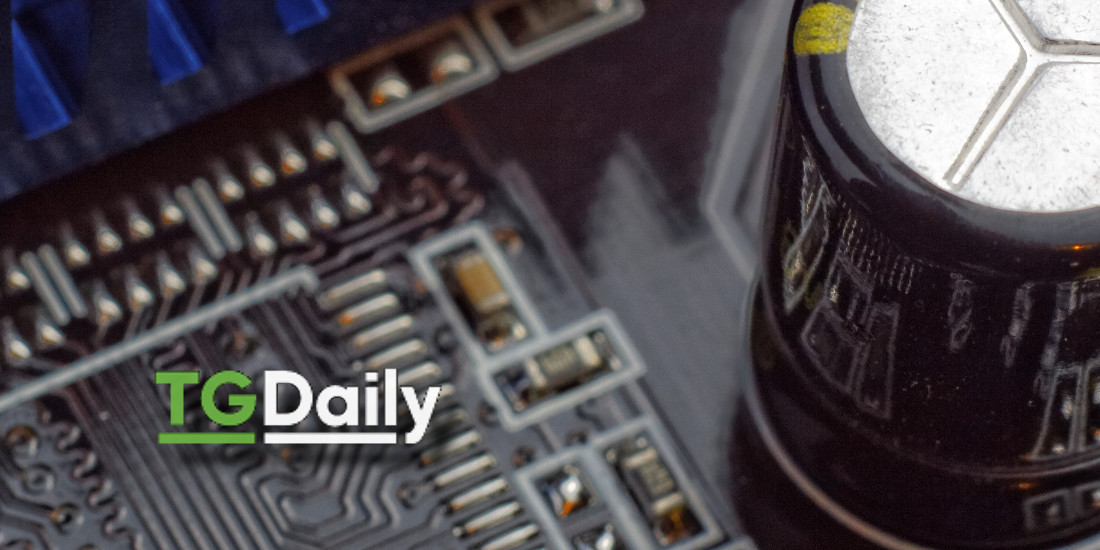
So let’s just come right out and say it: 3D printing is big. Really big.
Three-dimensional printing is based on what is known as additive manufacturing — meaning basically that instead of creating a detailed object by whittling away at pieces of a block of material, the way a sculptor would, you create the object by building up tiny pieces of it from scratch. A 3D printer reads the data encapsulated by a CAD drawing and translates into a series of cross-sections, which it builds up via successive layers of liquid, powder or metal, and ultimately joins or fuses automatically to create the final shape.
Three-dimensional printing technology is just 20 years old, but already, it’s changing the face of manufacturing, and is believed by many to be a technology as potentially significant as the home computer.
One of the publications that has followed the evolution and implications of 3D printing most closely is The Economist, which last year had this to say on the subject: “Three-dimensional printing makes it as cheap to create single items as it is to produce thousands and thus undermines economies of scale. It may have as profound an impact on the world as the coming of the factory did…. Just as nobody could have predicted the impact of the steam engine in 1750 — or the printing press in 1450, or the transistor in 1950 — it is impossible to foresee the long-term impact of 3D printing. But the technology is coming, and it is likely to disrupt every field it touches.”
There are those who see three-dimensional printing as a technology with the power to knock out whole classes of jobs in manufacturing — the fabricating machines owned by Ohio-based Rapid Quality Manufacturing, for example, run 24 hours a day, unattended.
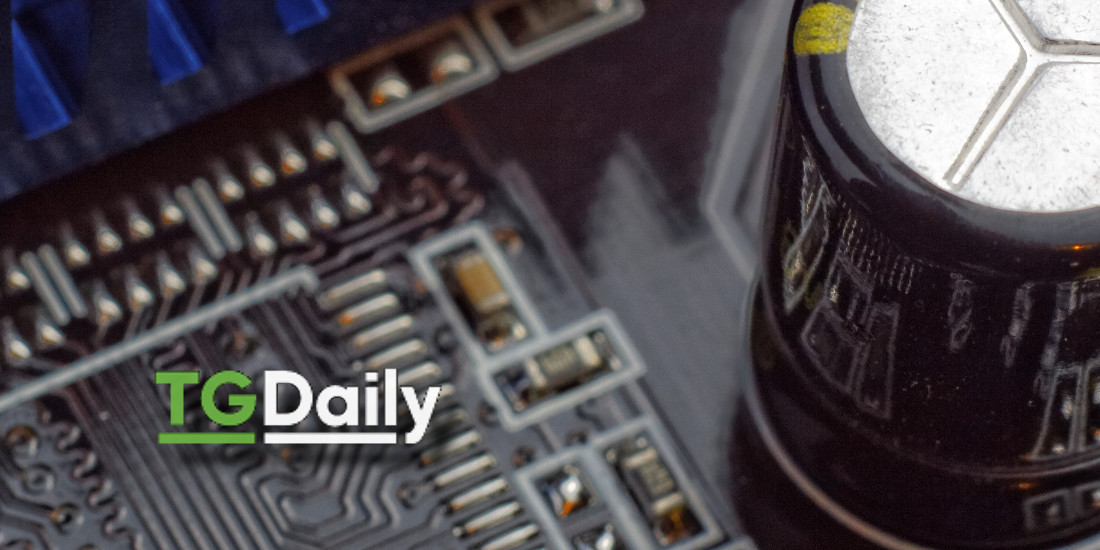
It seems likely that three-dimensional printing will, at the very least, decentralize manufacturing by reversing the urbanization that tends to accompany industrialization (not to mention the outsourcing of manufacturing to countries where labor is cheap).
But with the loss of manufacturing jobs comes huge possibilities for, well, pretty much everything else.
There are those focused on sustainable development in the Third World who believe that the addition of a community-owned village fabricator, in conjunction with open source software, could radically shift the economic equation in favor of people who lack the resources to purchase, say, a ready-made wind power system.
Others believe that with a price tag of around $5,000 for a small, basic model — or around half that, if you’re willing to build it yourself — the tech could kick off a home revolution, growing into a community of enthusiasts who share designs for 3D objects and even modify the machines for themselves. (These machines are even capable of producing back up parts for themselves.) Even today, online services such as Shapeways offer the average Joe and Jane the ability to design and affordably produce objects in a wide range of materials, with no virtually no training and at accessible price points.
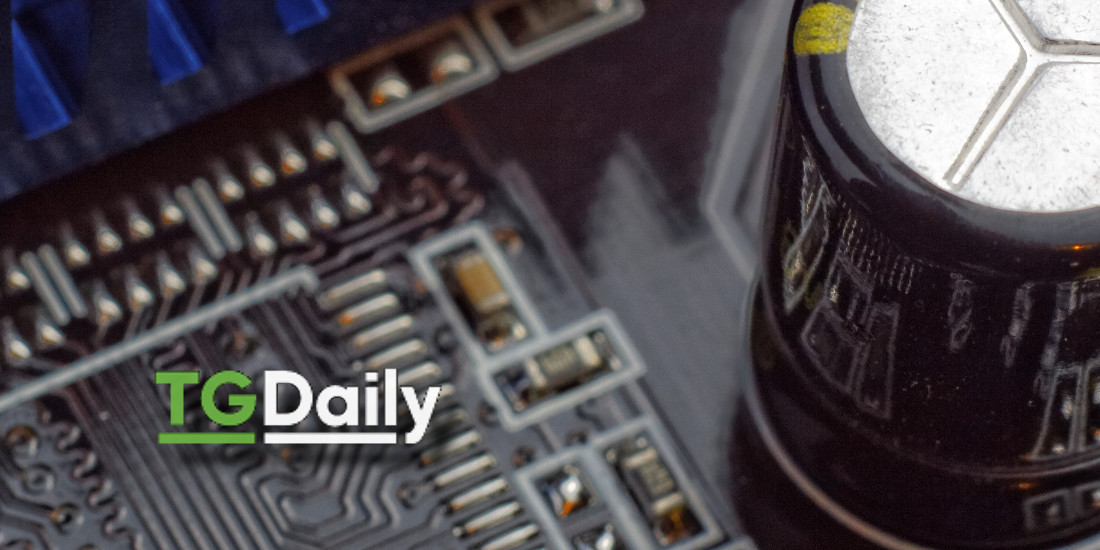
It’s worth pointing out that a home-fabricating revolution, accompanied by decentralized, local manufacturing, has the potential to significantly reduce the carbon footprint of the average widget. (Especially with printers that utilize materials like plant-based plastics.)
One of the most significant areas of eco-potential for three-dimensional printing technology is in green building. Currently, green homes built through the process of prefabrication save considerable resources over the average site-built home, but they’re often shipped over long distances, upping the carbon footprint of even the most environmentally friendly materials.
A mobile print pavilion, such as a scaled up version of the Kamermaker, which recently made its debut in the Netherlands, could fit the bill, combining the capabilities of the current behemoth in the fabrication landscape, the D-Shape, with the ability to go where it’s needed.
The D-Shape uses very low levels of energy as compared to traditional manufacturing processes, and creates a kind of artificial sandstone similar to marble, effectively returning any type of sand, dust or gravel back to its original state as a compact stone. (So when Jimi Hendrix sang about castles made of sand, hey, maybe he was on to something).
Monolite, the company behind the printer, sees the D-Shape as providing low-cost access to building for people in need around the world. But the company would also be happy to fab an super-artistic staircase for you, or even a futuristic gazebo, such as the Radiolaria (pictured).
As with any truly revolutionary tech, the implications aren’t likely to be all positive — consider, for instance, the nightmare of intellectual property in the age of home fabrication, printed-at-home drugs, or even the three-dimensionally printed gun. But as green tech geeks, we’re inclined toward optimism, and will be closely following the progress of three-dimensional printing tech in promoting the greener good.