Researchers at the Georgia Tech Research Institute (GTRI) have created a new prototype radiation detection device for use at ports, border crossings, airports and elsewhere.
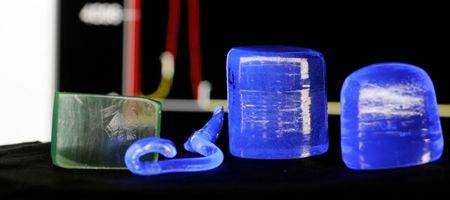
Using new materials and nanotechnology techniques, they’ve developed the Nano-photonic Composite Scintillation Detector, which combines rare-earth elements and other materials at the nanoscale to improve sensitivity, accuracy and robustness.
“US security personnel have to be on guard against two types of nuclear attack – true nuclear bombs, and devices that seek to harm people by dispersing radioactive material,” says co-principal researcher Bernd Kahn. “Both of these threats can be successfully detected by the right technology.”
There are currently two common types of radiation detectors: scintillation detector, which usually employ a single crystal of sodium iodide or a similar material, and solid-state detectors based on semiconducting materials such as germanium.
Both technologies can detect gamma rays and subatomic particles emitted by nuclear material, but have drawbacks. The large sodium iodide crystals required for scintillation detectors are typically fragile, cumbersome, difficult to produce and extremely vulnerable to humidity.
Meanwhile, germanium-based solid-state detectors offer better identification of different kinds of nuclear materials – but are less sensitive.
The Georgia Tech team decided to got for the scintillation approach over solid-state, and developed a composite material – composed of nanoparticles of rare-earth elements, halides and oxides – capable of creating light.
“A nanopowder can be much easier to make, because you don’t have to worry about producing a single large crystal that has zero imperfections,” says co-principal investigator Brent Wagner.
Scattering effects are reduced with the nanopowder, as the particles are significantly smaller than the wavelength of incoming gamma rays.
“We’re optimistic that we’ve identified a productive methodology for creating a material that could be effective in the field,” says Wagner.
“We’re continuing to work on issues involving purity, uniformity and scaling, with the aim of producing a material that can be successfully tested and deployed.”