Stanford engineers have developed new peel-and-stick solar panels that they say can be applied to almost any surface.
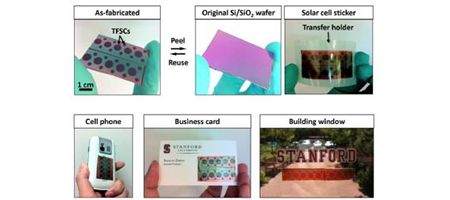
Unlike standard thin-film solar cells, they don’t require any direct fabrication on the final carrier substrate – a very important development. Thin-film photovoltaic cells are traditionally fixed on rigid silicon and glass substrates, greatly limiting their uses.
“Nonconventional or ‘universal’ substrates are difficult to use for photovoltaics because they typically have irregular surfaces and they don’t do well with the thermal and chemical processing necessary to produce today’s solar cells,” says assistant professor of mechanical engineering Xiaolin Zheng.
“We got around these problems by developing this peel-and-stick process, which gives thin-film solar cells flexibility and attachment potential we’ve never seen before, and also reduces their general cost and weight.”
The team’s already successfully slapped its solar cells onto paper, plastic and window glass.
The new process involves a unique silicon, silicon dioxide and metal sandwich. First, a 300-nanometer film of nickel is deposited on a silicon/silicon dioxide (Si/SiO2) wafer, and then thin-film solar cells are deposited on the nickel layer via standard fabrication techniques, and covered with a layer of protective polymer.
A thermal release tape is then attached to the top of the thin-film solar cells to help them transfer off the production wafer and onto a new substrate.
To peel the solar cell from the wafer, the wafer’s submerged in water at room temperature and the edge of the thermal release tape is peeled back slightly, allowing water to seep into and penetrate between the nickel and silicon dioxide interface. The solar cell is thus freed from the hard substrate but still attached to the thermal release tape.
Once the tape and solar cell are heated to 90°C for a few seconds, the cell can be applied to virtually any surface using double-sided tape or other adhesive. Finally, the thermal release tape is removed, leaving just the solar cell.
“Now you can put them on helmets, cell phones, convex windows, portable electronic devices, curved roofs, clothing – virtually anything,” says Zheng.
The researchers allo believe the process could be applied to thin-film electronics, including printed circuits and ultra thin transistors and LCDs.
“Obviously, a lot of new products – from ‘smart’ clothing to new aerospace systems – might be possible by combining both thin-film electronics and thin-film solar cells,” he says.
“And for that matter, we may be just at the beginning of this technology. The peel-and-stick qualities we’re researching probably aren’t restricted to Ni/SiO2. It’s likely many other material interfaces demonstrate similar qualities, and they may have certain advantages for specific applications. We have a lot left to investigate.”