First thing every morning, the engineering team for NASA’s Magnetospheric Multiscale mission gathers for a 10-minute meeting. A white board sits at the front of the room with the day’s assignments – who will wrap tape around the wires, which instruments need to be installed where, which observatory needs to undergo its next test.
This is the nerve center for the MMS engineers and technicians at NASA’s Goddard Space Flight Center in Greenbelt, Md. Goddard is tasked with an unprecedented feat for the center: building four identical observatories simultaneously. The four spacecraft will launch together on a single rocket and then maneuver out into a pyramid configuration to orbit Earth.
On its journey, MMS will observe a little-understood, but universal phenomenon called magnetic reconnection, responsible for dramatic re-shaping of the magnetic environment near Earth, often sending intense amounts of energy and fast-moving particles off in a new direction. Not only is this a fundamental physical process that occurs throughout the universe, it is also one of the drivers of space weather events at Earth. To truly understand the process, requires four identical spacecraft to track how such reconnection events move across and through any given space.
Building four spacecraft at once has many advantages. It saves on time and mission cost. However, such a massive undertaking requires meticulous logistical planning.
“This is the first time NASA has ever built four satellites simultaneously like this,” said Craig Tooley, project manager for MMS at Goddard. “It feels like we’re planning a giant game of musical chairs to produce multiple copies of a spacecraft. One instrument deck might be 2/3 finished, while another one is 1/3 finished, and the same people will have to test a nearly complete deck one day, and install large components on another one another day.”
One of the earliest important feats for this group of engineers and technicians came during the design phase. Each spacecraft must carry, in addition to the navigational and power instruments, 25 scientific instruments. These had to be carefully laid out so that each instrument had a full range of view and so that the eight booms sticking out from the spacecraft would not interfere with any other instrument’s line of sight or electromagnetic systems.
The instruments themselves were constructed and assembled around the world at a variety of institutions. Each one was then shipped to Goddard to be placed in its specific spot on what’s called the instrument deck.
Each spacecraft contains two decks, one for the science instruments and one for the power and navigation tools. The decks are made of two aluminum sheets bonded on either side of an inner, honey-comb-shaped layer also made of aluminum. The second deck is called the spacecraft deck. It supports a power box, a computer, transmitters and receivers, a star tracker to help with orientation, and batteries for power during solar eclipses. The two decks are attached to struts, with the instruments facing each other in the middle. A central thrust tube carries four propellant tanks. Solar arrays span the space in between the decks.
Above and beyond installing all the instruments, each spacecraft sports hundreds of wires that connect the instruments to the main computer and power sources, as well as the instruments to each other. Not only does this entire harness need to be installed, but technicians must hand wrap every wire in insulation to shield the sensitive instruments from electrical interference.
“The sheer amount of labor just to put in all these connections is stunning,” said Gary Davis, spacecraft systems engineer for MMS at Goddard. “When you’re building four at a time, the team doesn’t get a break. If one spacecraft is in testing, then the team works on a different observatory.”
It is just this kind of juggling that must be done every day: Which engineer goes where and which spacecraft goes into which cleanroom, as each follows its journey of instrument insertion, wiring, testing, and more engineering.
In addition to the physical engineering, the software on board must be tested too. Such testing requires that the spacecraft be powered up, which consequently prohibits simultaneous mechanical or electrical work.
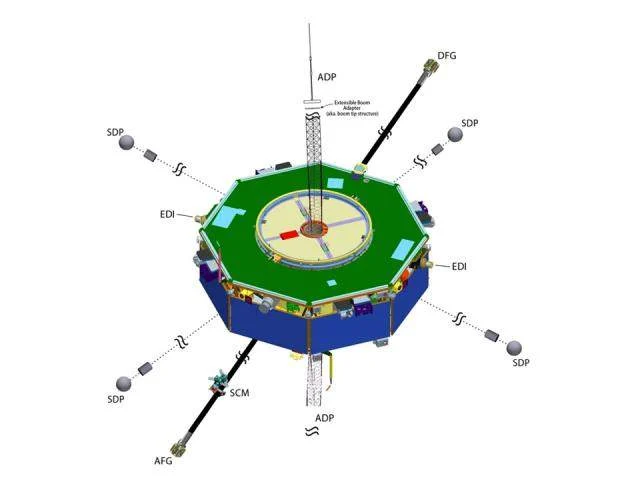
“The work is so interesting and even fun, but with a schedule this complicated we have to make some careful choices about who is doing what,” said Davis. “We also have to make sure the team pushes ahead at the right pace. We want to move ahead as quickly as safely possible, but no faster.” Safety is, indeed, the team’s number one concern.
Since May 2013 all four observatories have been integrated with all necessary science instruments and flight hardware. Since then, they have undergone a wide range of ground tests – rigorous electrical, vibration, acoustics and thermal testing to ensure they can withstand the launch and extreme environments of space and launch conditions.
After testing is complete, the four observatories will be shipped, two at a time, isolated on a truck bed with exquisite air and temperature control, to Astrotech in Titusville, Fla., for launch processing and then to NASA’s Kennedy Space Center in Florida for launch. Engineers will complete the final closeout. The propellant will be loaded into the tanks. The spacecraft will be carefully encapsulated into the rocket fairing for launch. And, at last, after four years of engineering, the four obseratories will finally fly.