Completely surrounded by a massive 20-foot-high structure called the crew module static load test fixture, the Orion crew module is being put through a series of tests that simulate the massive loads the spacecraft would experience during its mission.
Orion is NASA’s new exploration spacecraft, designed to carry humans farther into space than ever before. During its first flight test next year, Exploration Flight Test-1 (EFT-1), it will travel 3,600 miles into space and return to Earth. This will allow NASA to evaluate Orion’s performance in preparation for future deep space journeys.
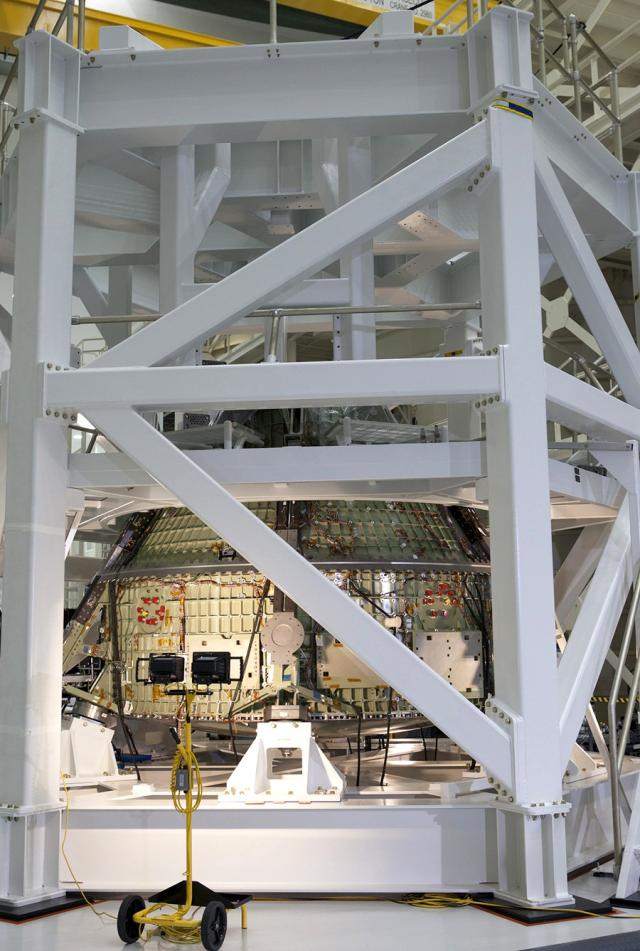
Lockheed Martin Space Systems began static loads testing May 3 on the Orion EFT-1 crew module inside the Operations and Checkout (O&C) Building at Kennedy Space Center in Florida. Technicians will use hydraulic cylinders to slowly apply pressure to various areas of the vehicle to simulate the loads it will be exposed to at different phases of the mission.
The tests will run throughout May and June, with different phases simulating launch, ascent, launch abort, launch abort system separation, reentry and landing. Lockheed Martin is conducting the tests based on a set of prototype flight requirements.
“We perform these tests to ensure the structural integrity of the crew module,” said Carlos Garcia, a test engineer in the Orion Production Office at Kennedy.
During the months and weeks leading up to the static tests, NASA and Lockheed Martin engineers and technicians configured Orion for its placement on the test fixture and staged the associated equipment and hardware that would be needed to verify Orion is one step closer to being flight ready.
The pressurized crew module will be put through a series of eight different load tests, each one taking up to three days to complete. Each test will focus on a different area of the crew module and require a different configuration of the hydraulic actuators that are attached to it.
“The first four tests represent the ascent regime and the last four represent the re-entry flight regime,” Garcia said.
One of the tests also will allow engineers to test repairs they made to cracks in the crew module’s aluminum bulkhead that occurred last November. The cracks appeared as the vehicle was being pressurized for a proof pressure test aimed at verifying the vehicle’s structural integrity and validating engineering models used to design it.
Repairs were made to the vehicle, and the series of tests provides an opportunity to repeat the proof pressure tests to ensure that they will hold, according to Garcia.
More than 1,600 strain gauges have been attached to Orion’s external surface and inside the crew module to verify the crew cabin structure. Cameras have been placed around Orion to record any movement during the load tests.
Several other sensors have been attached at various locations around and beneath Orion to measure any deflection or expansion during the repeat of the proof pressure test.
“The set of tests are critical to build the foundation for the future of spaceflight,” said Steve Cook, the Lockheed Martin Project Orion mechanical test engineer lead. “We learn from our successes and challenges.”
Lockheed Martin and NASA engineers will monitor the tests from the completely refurbished lower level of the high bay, called the “tunnel,” as its control room to fully execute the tests and compare the results with stress model predictions.
The Operations and Checkout Building serves as the final assembly and checkout facility for Orion.
EFT-1 is scheduled to launch atop a United Launch Alliance Delta IV heavy rocket from Launch Complex 41 at Cape Canaveral Air Force Station in Florida in 2014. The agency’s Space Launch System rocket will begin launching Orion in 2017.