Building a base on the moon could theoretically be made much simpler by using a 3D printer to construct it from local materials.
Interestingly, the concept was recently endorsed by none other than the European Space Agency (ESA) which is now collaborating with architects Foster + Partners to gauge the feasibility of 3D printing using lunar soil.
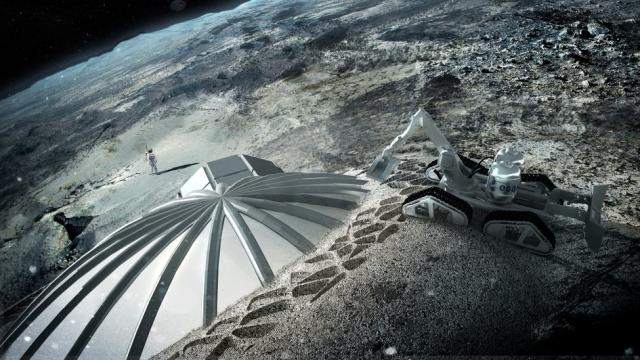
“Terrestrial 3D printing technology has produced entire structures,” explained Laurent Pambaguian, heading the project for ESA.
“Our industrial team investigated if it could similarly be employed to build a lunar habitat.”
According to Pambaguian, Foster + Partners has devised a weight-bearing “catenary” dome design with a cellular structured wall to help shield against micrometeoroids and space radiation – incorporating a pressurized inflatable to shelter astronauts.
Meanwhile, a hollow closed-cell structure – somewhat reminiscent of bird bones – provides a combination of strength and weight. The base’s design was guided in turn by the properties of 3D-printed lunar soil, with a 1.5 tonne building block produced as a demonstration.
“3D printing offers a potential means of facilitating lunar settlement with reduced logistics from Earth,” said Scott Hovland of ESA’s human spaceflight team.
“The new possibilities this work opens up can then be considered by international space agencies as part of the current development of a common exploration strategy.”
The UK’s Monolite supplied the D-Shape printer, with a mobile printing array of nozzles on a 6 m frame to spray a binding solution onto a sand-like building material.
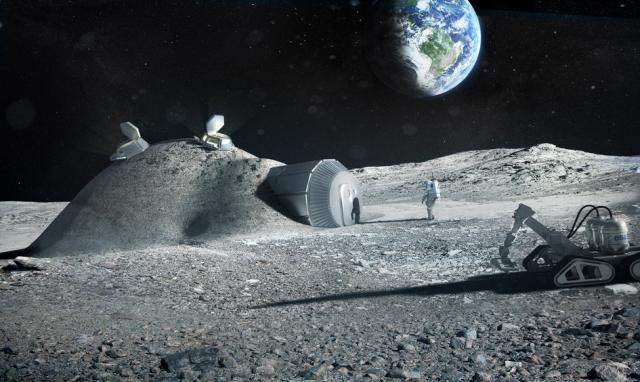
Essentially, 3D “printouts” are built up layer by layer – the company more typically uses its printer to create sculptures and is working on artificial coral reefs to help preserve beaches from energetic sea waves.
“First, we needed to mix the simulated lunar material with magnesium oxide. This turns it into ‘paper’ we can print with,” explained Monolite founder Enrico Dini.
“Then for our structural ‘ink’ we apply a binding salt which converts material to a stone-like solid. Our current printer builds at a rate of around 2 m per hour, while our next-gen design should attain 3.5 m per hour, completing an entire building in a week.”