A Detroit inventor has found a way to make steel seven percent stronger than any steel on record, offering the promise of lighter, thinner car bodies and stronger armored vehicles.
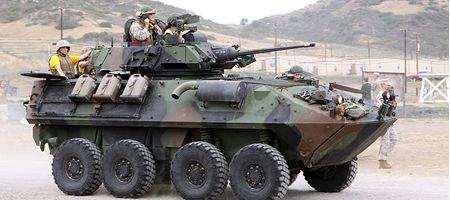
When self-taught metallurgist Gary Cola approached engineers at Ohio State University with his process – which takes just ten seconds – they thought he must have made a mistake.
“The process that Gary described – it shouldn’t have worked,” says associate professor of materials science and engineering Suresh Babu. “I didn’t believe him. So he took my students and me to Detroit.”
Cola’s process involves rapid heating and cooling, which changes the microstructure inside the alloy to make it stronger and less brittle. At his proprietary lab setup, where rollers carried steel sheets through flames as hot as 1100 degrees Celsius and then into a cooling liquid bath.
The process takes just ten seconds, while existing methods involve keeping the steel at around 900 degrees Celcius for hours or even days.
And the resulting steel, now trademarked as Flash Bainite, has tested stronger and more shock-absorbing than the most common titanium alloys used by industry.
Babu’s tests confirmed that it was seven percent stronger than martensitic advanced high-strength steel. It can be drawn – thinned and lengthened – 30 percent more than martensitic steels without losing its strength.
This would allow carmakers to build frames that are up to 30 percent thinner and lighter without compromising safety, or reinforce an armored vehicle without weighing it down.
“Steel is what we would call a mature technology. We’d like to think we know most everything about it,” says Babu. “If someone invented a way to strengthen the strongest steels even a few percent, that would be a big deal. But seven percent? That’s huge.”
Using an electron microscope, Babu’s team discovered that the process formed martensite microstructure inside the steel. But they also saw another form called bainite microstructure, scattered with carbon-rich compounds called carbides.
“We think that, because this new process is so fast with rapid heating and cooling, the carbides don’t get a chance to dissolve completely within austenite at high temperature, so they remain in the steel and make this unique microstructure containing bainite, martensite and carbides,” says Babu.