Cornell bioengineers and physicians have created a fully-functioning artificial ear, using 3D printing and injectable molds.
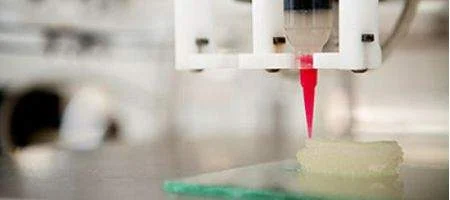
Over a three-month period, the ears grew cartilage to replace the collagen that was used to mold them. The end result looks and acts like a natural ear.
“This is such a win-win for both medicine and basic science, demonstrating what we can achieve when we work together,” says associate professor of biomedical engineering Lawrence Bonassar.
The ear could give new hope to thousands of children born with a congenital deformity called microtia, as well as peoplewho have lost part or all of their external ear in an accident or from cancer. Currently, replacement ears are usually constructed with materials that have a Styrofoam-like consistency, or sometimes, built painfully from a patient’s rib.
To make the ears, Bonassar and colleagues started with a digitized 3D image of a human ear, and converted the image into a digitized ‘solid’ ear using a 3D printer to assemble a mold. The collagen served as a scaffold upon which cartilage could grow.
The process is fast, says Bonassar: “It takes half a day to design the mold, a day or so to print it, 30 minutes to inject the gel, and we can remove the ear 15 minutes later. We trim the ear and then let it culture for several days in nourishing cell culture media before it is implanted.”
The team says it may be possible to try the first human implant of a Cornell bioengineered ear in as little as three years.