Future lunar missions may be fueled by gas stations in space, according to MIT engineers: A spacecraft might dock at a propellant depot, somewhere between the Earth and the moon, and pick up extra rocket fuel before making its way to the lunar surface.
Orbiting way stations could reduce the fuel a spacecraft needs to carry from Earth — and with less fuel onboard, a rocket could launch heavier payloads, such as large scientific experiments.
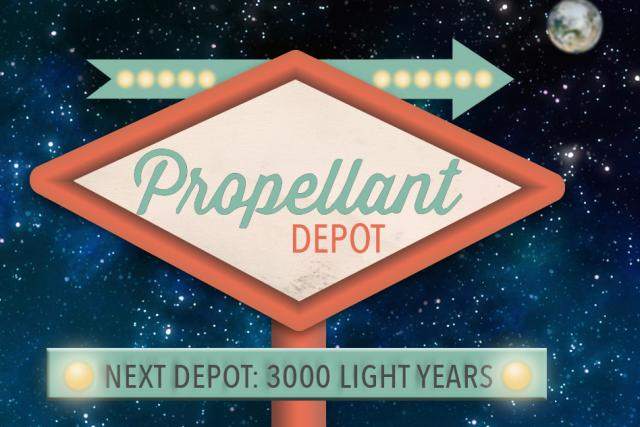
Over the last few decades, scientists have proposed various designs, such as building a fuel-manufacturing station on the moon and sending tankers to refill floating depots. But most ideas have come with hefty price tags, requiring long-term investment.
The MIT team has come up with two cost-efficient depot designs that do not require such long-term commitment. Both designs take advantage of the fact that each lunar mission carries a supply of “contingency propellant” — fuel that’s meant to be used only in emergencies. In most cases, this backup fuel goes unused, and is either left on the moon or burned up as the crew re-enters the Earth’s atmosphere.
Instead, the MIT team proposes using contingency propellant from past missions to fuel future spacecraft. For instance, as a mission heads back to Earth, it may drop a tank of contingency propellant at a depot before heading home. The next mission can pick up the fuel tank on its way to the moon as its own emergency supply. If it ends up not needing the extra propellant, it can also drop it at the depot for the next mission — an arrangement that the team refers to as a “steady-state” approach.
A depot may also accumulate contingency propellant from multiple missions, part of an approach the researchers call “stockpiling.” Spacecraft heading to the moon would carry contingency propellant as they normally would, dropping the tank at a depot on the way back to Earth if it’s not needed; over time, the depot builds up a large fuel supply. This way, if a large lunar mission launches in the future, its rocket wouldn’t need a huge fuel supply to launch the heavier payload. Instead, it can stop at the depot to collect the stockpiled propellant to fuel its landing on the moon.
“Whatever rockets you use, you’d like to take full advantage of your lifting capacity,” says Jeffrey Hoffman, a professor of the practice in MIT’s Department of Aeronautics and Astronautics. “Most of what we launch from the Earth is propellant. So whatever you can save, there’s that much more payload you can take with you.”
Hoffman and his students — Koki Ho, Katherine Gerhard, Austin Nicholas, and Alexander Buck — outline their depot architecture in the journal Acta Astronautica.
Pickup and drop-off in space
The researchers came up with a basic mission strategy to return humans to the moon, one slightly different from that of the Apollo missions. During the Apollo era, spacecraft circled close to the lunar equator — a route that required little change in direction, and little fuel to stay on track. In the future, lunar missions may take a more flexible approach, with the freedom to change course to explore farther reaches of the moon — such as the polar caps, for evidence of water — a strategy that would require each spacecraft to carry extra fuel to change orbits.
Working under the assumption of a more global exploration strategy, the researchers designed a basic architecture involving a series of stand-alone missions, each exploring the surface of the moon for seven to 14 days. This mission plan requires that a spacecraft returning to Earth must change its orbital plane when needed. Under this basic scenario, missions could operate under existing infrastructure, without fuel depots, meaning that each spacecraft would carry its own supply of contingency propellant.
The researchers then drew up two depot designs to improve the efficiency of the basic scenario. In both designs, depots would be stationed at Lagrange points — regions in space between the Earth, moon, and sun that maintain gravitational equilibrium. Objects at these points remain in place, keeping the same relative position with respect to the Earth and the moon.
Hoffman says that ideally, transferring fuel between the depot and a spacecraft would simply involve astronauts or a robotic arm picking up a tank. The alternative — siphoning fuel from tank to tank like you would for your car — is a bit trickier, as liquid tends to float in a gravity-free environment. But, Hoffman says, it’s doable.
“In building the International Space Station, every time a new module is added, we’ve had to hook up new fluid connections,” Hoffman says. “It’s not a trivial design problem, but it can be done.”
‘Creating value … against political uncertainty’
The main drawbacks for both depot designs include maintenance; keeping depots within the Lagrange point; and preventing a phenomenon, called “boil-off,” in which fuel that’s not kept at cold-enough temperatures can boil away. If scientists can find ways around these challenges, Hoffman says, gas stations in space could be an efficient way to support large lunar explorations.
“One of the problems with large space programs is, you invest a huge amount in building up the infrastructure, and then a program gets canceled,” Hoffman says. “With depot architectures, you’re creating value which is robust against political uncertainty.”
The paper came out of two MIT classes taught by Hoffman: 16.851 (Satellite Engineering) and 16.89 (Space Systems Engineering), in which students also looked at redesigning a lunar lander and evaluated different approaches to landing on the moon.
James Head, a professor of geological sciences at Brown University, says the group’s two approaches optimize the possibility of both near-lunar missions and more ambitious, longer-duration missions to more distant destinations.
“Currently, NASA is once again considering circumlunar human operations and developing architectures for moving on to Mars,” Head says. “So this paper is extremely important and timely in the context of developing NASA plans for human exploration beyond low Earth orbit.”